Desiccant Air Dryers
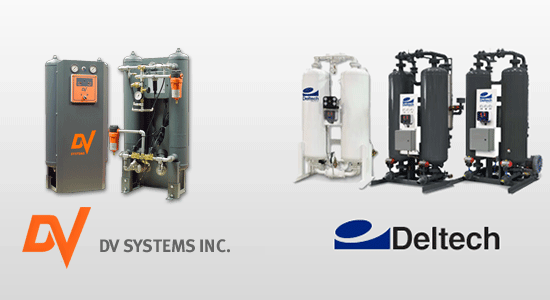
Desiccant Dryers
Regenerative desiccant dryers adsorb moisture on solid desiccants, such as activated alumina, silica gel, or molecular sieves. Two desiccant-packed towers operate alternately; compressed air flows through the desiccant in one tower while the desiccant in the other tower is dried, or regenerated.Regenerative desiccant dryers supply the lowest dew point, usually -40°F but as low as -100°F. They are also the most expensive, so specify a regenerative desiccant dryer only when the application calls for maximum dew point performance. Regenerative dryers are often used to protect instrumentation and control systems, laboratory equipment, and moisture‐sensitive processes and materials. They also protect outdoor lines from freezing in severe weather conditions.
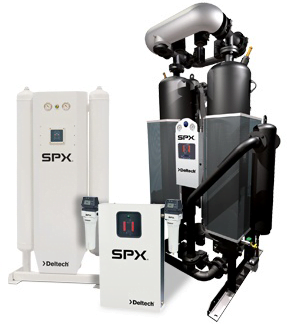
There are three different methods to regenerate the saturated desiccant bed: by a purge of dry air from the operating tower, by internal heaters, or by an external heat source. Here are the pluses and minuses of each:
- Heatless dryers use a purge of compressed air from the active tower, expanded to atmospheric pressure to dry the desiccant. It is a simple process, with the purge air vented to atmosphere. The units require little maintenance and, because they do not deal with the high voltages or high temperature, are quite safe. Heatless dryers are also the least expensive regenerative dryers, so they are a good choice for smaller systems with sufficient excess air capacity. Unfortunately, the purge requires 15 to 18% of air capacity, which means high operating costs in largersystems. Often the expense associated with lost compressor horsepower restricts heatless dryers to systems smaller than approximately 2,000 scfm. This is increasingly the case as energy costs rise and companies strive to minimize power consumption.
- Heated regenerative desiccant dryers use electrical resistance or steam heat to dry the desiccant bed, so only about 4.5% purge air is needed to drive off the water. These units initially cost more than heatless dryers because they have additional components and more complex controls. Skilled personnel are also required for maintenance. Heated dryers are predominantly used in the 500-3,000 scfm range. However, the specific application always dictates the best choice.
- Blower-purge compressed air dryers use an external blower to force heated atmospheric air through the regenerating tower. This dries the bed without requiring compressed air. However, blower units require the highest initial investment among regenerative dryers. For two reasons, they are used almost exclusively in large systems above 3,000 scfm. One, the cost of purge air required by the heatless type dryer is proportional to the size of the system, making the expense of purging prohibitive in large installations. Two, conducting heat evenly through an Internally Heated type dryer with a large desiccant bed is a technical challenge that requires many embedded heaters; to regenerate a large desiccant bed it is much simpler to evenly heat the bed with a blower.
The desiccant in heatless dryers lasts ten to fifteen years with an oil-free compressor and five to ten years with a lubricated compressor and a good prefilter. Oil contamination destroys the sensitive desiccant in about two to three weeks. Heated dryers tend to accelerate the aging process of adsorbent desiccant. Typically, new desiccant material is needed every three to five years.